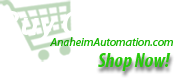
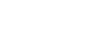
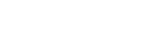


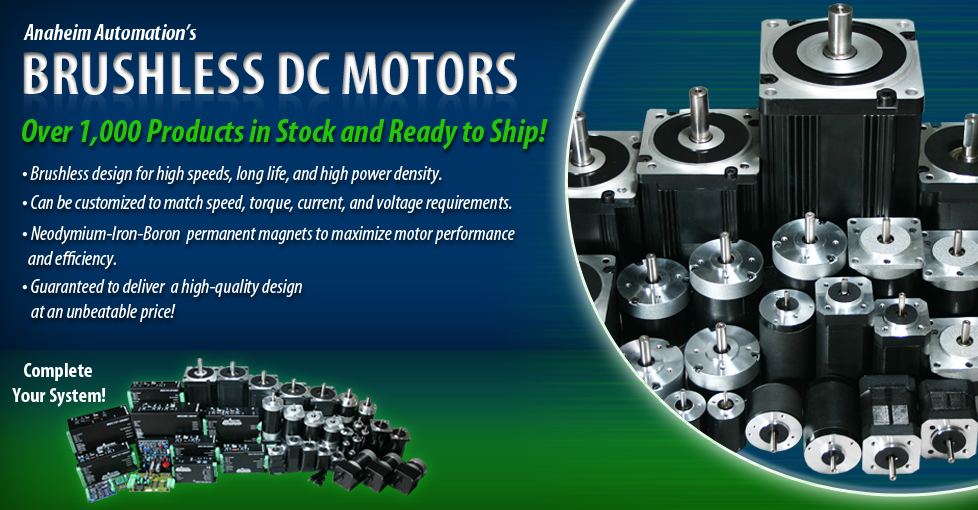
What is a Brushless DC Motor?
A Brushless DC Motor (also known as a BLDC Motor), is a synchronous electric motor powered by a direct current. As the name implies, the Brushless DC Motor does not operate using brushes; rather it operates with a controller via electronic commutation.
Block Diagram for a Brushless DC Motor
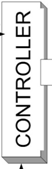
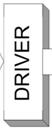
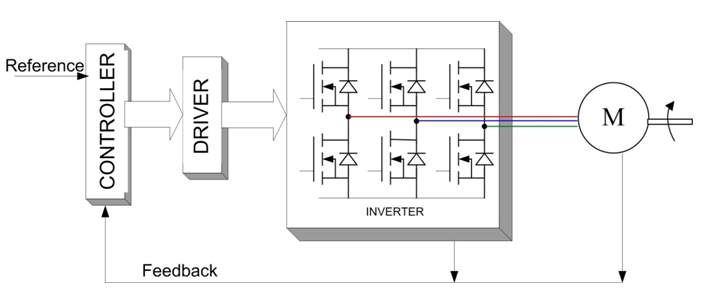
How does a Brushless DC Motor Work?
A Brushless DC Motor is operated by means of an electronic six-step commutation system. Unlike its Brush DC Motor counterparts, the Brushless DC Motor does not contain any carbon brushes. Instead, the electromagnets within the motor remain stationary along with the armature, while the encased permanent magnets rotate, generating torque. The Brushless DC Motor is synchronous; both the stator and the magnetic field generate the same frequency, therefore avoiding any type of "slip" most induction motors exhibit.
What is Six-Step Commutation?
Six-step commutation is a cost-effective means of electronic commutation, due to the simple and relatively inexpensive feedback and drive devices. In six-step commutation, only two out of the three Brushless DC Motor windings are used at a time. Steps are equivalent to 60 electrical degrees, so six steps makes a full, 360 degree rotation. One full 360 degree loop is able to control the current, due to the fact that there is only one current path. Six-step commutation is typically useful in applications requiring high speed and commutation frequencies. A six-step Brushless DC Motor usually has lower torque efficiency than a sine-wave commutated motor.
How is a Brushless DC Motor Controlled?
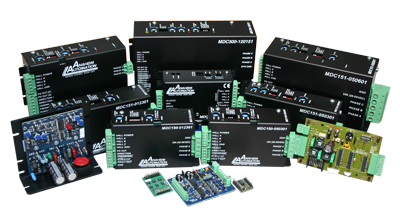
An electronic Brushless DC Controller (also known as a Driver, or Electronic Speed Controller), replaces the mechanical commutation system utilized by a Brush DC Motor, and is required by most Brushless DC Motors to operate. In a Brushless DC Motor controller, either a Hall Effect Sensor or Back EMF (Electromotive Force) is used to identify the position of the rotor. Understanding the orientation of the rotor is crucial to operating the Brushless DC Motor.
The Hall Effect uses three hall sensors within the Brushless DC Motor to help detect the position of the rotor. This method is primarily used in speed detection, positioning, current sensing, and proximity switching. The magnetic field changes in response to the transducer that varies its output voltage. Feedback is created by directly returning a voltage, because the sensor operates as an analogue transducer. The distance between the Hall plate and a known magnetic field can be determined with a group of sensors, and the relative position of the magnet can be deduced. A Hall sensor can act as an on/off switch in a digital mode when combined with circuitry.
Back EMF, also known as the Counter-Electromotive Force, is caused by a changing electromagnetic field. In a Brushless DC Motor, back EMF is a voltage that occurs where there is motion between the external magnetic field and the armature of the motor. In other words, the voltage is developed in an inductor by an alternating or pulsating current. The polarity of the voltage is constantly the reverse of the input voltage. This method is commonly used to measure the position and speed of the Brushless DC Motor indirectly, and due to the lack of Hall Sensors within the controller, these are often referred to as sensorless controllers.
Optical Encoders can also be added to the Brushless DC Motor, allowing both direction and speed to be determined. More precise applications may use Optical Encoders with a third index signal, to determine pulse per revolution.
Physical Properties of a Brushless DC Motor
The Brushless DC Motor consists of a rotating rotor, Neodymium Iron Boron magnets, and a stator. Brushless DC Motors are considered to be an "inside-out" version of a Brush DC Motor; the commutator and brushes are nonexistent, and the windings are located externally, connected to the controller. There are typically two different construction types for the Brushless DC Motor: inrunner and outrunner configurations. The inrunner configuration consists of three stator windings located around the rotor, with permanent magnets as a part of the rotor. The outrunner has a reversed relationship between the magnets and the coils. The permanent magnets rotate inside a suspended rotor surrounding the core of the Brushless DC Motor.
Internally, a 3-phase motor can be configured to a "Wye" or "Delta" configuration. The primary advantage to the "Wye" configuration, also known as the Star configuration, is that the phase-to-neutral voltage is equal in all three legs. The arrangement is a parallel circuit in a shape of the letter Y, where all windings are connected at a central point, and power is applied to the remaining windings.
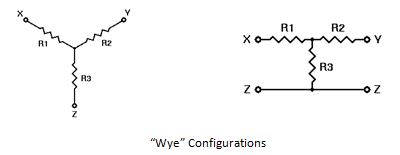
The Delta configuration creates a triangle-like figure, making it a series circuit. This configuration applies power to each of the connections.
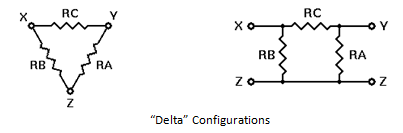
How to Select a Brushless DC Motor
Selecting the appropriate Brushless DC Motor requires knowing the requirements of the application, such as torque, speed, size, power, length, etc. While determining which Brushless DC Motor best fits the requirements, the controller must be considered as well, as this goes hand in hand with the operation of the Brushless DC Motor.
Lastly, environment is important to consider. Applications requiring a harsh, damp environment may require motors with specific IP ratings. For more detailed information on this subject, see Brushless DC Motor Environmental Considerations.
Brushless DC Motor Applications
The cost of the Brushless DC Motor has declined since its introduction, due to advancements in materials and design. This decrease in price, coupled with the many advantages it has over the Brush DC Motor, makes the Brushless DC Motor a popular component in many different applications. Applications that utilize the Brushless DC Motor include, but are not limited to:
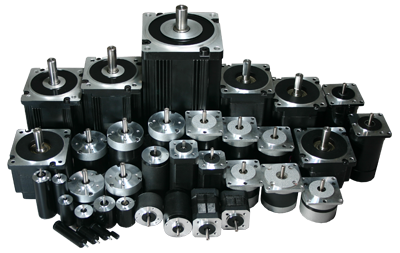
• Instrumentation |
• Medical |
• Appliances |
• Automotive |
• Factory Automation Equipment |
• Aerospace |
• Military |
Advantages of a Brushless DC Motor
The absence of brushes in a Brushless DC Motor is perhaps its greatest advantage. The carbon brushes within a Brush DC Motor wear out rapidly and need replacing, which can be costly in the long run. The Brushless DC Motor generates less noise, and is less prone to sparking due to the lack of a commutator. The Brushless DC Motor is typically smaller and lighter than the Brush DC Motor, making it ideal for applications where weight and space are important factors. The Brushless DC motor is cleaner, more powerful, and requires lower maintenance than does the Brush DC Motor. It has higher speed ranges, higher dynamic responses, and ultimately outlasts the Brush DC Motor in total operating hours.
Disadvantages of a Brushless DC Motor
There are numerous applications using a Brush DC Motor that could instead utilize the Brushless DC Motor. However a few factors might prevent the changeover. The first factor is start-up cost. Although the Brushless DC Motor is lower-maintenance than the Brush DC Motor, initial cost is more expensive, due to its advantageous construction. Second is complexity. A controller is required in order to operate a Brushless DC Motor, and is usually more convoluted than most controllers. A Brushless DC Motor also requires additional system wiring, in order to power the electronic commutation circuitry.
Lifetime of a Brushless DC Motor
The Brushless DC Motor is often considered superior over the Brush DC Motor for its substantially longer lifespan. If run within the given specifications, the Brushless DC Motor can last over 20,000 operating hours based on bearing life. Running a Brushless DC Motor outside of its specifications shortens this lifespan.
Required Maintenance of a Brushless DC Motor
Due to the lack of brushes or a commutator, there is nothing to replace within a Brushless DC Motor, making it extremely low maintenance. The only requirement is that the motor be run within proper specifications, and in a clean environment to ensure it does not overheat or result in system failure.
Brushless DC Motor Environmental Considerations
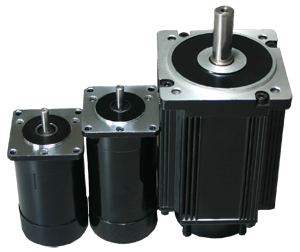
Precaution must be taken by the user with respect to the environment of the Brushless DC Motor system during operation, repair, and service. The environment in which a Brushless DC Motor is used, must be conducive to good general practices of electrical equipment. Do not run a Brushless DC Motor system near flammable gases, dust, oil, vapor or moisture. The Brushless DC Motor must be protected by a cover if operated outdoors, ensuring the motor receives adequate air flow and cooling. Any presence of moisture may result in system failure and/or electric shock. Therefore adequate care should be taken to avoid any interaction between the Brushless DC Motor and any kind of moisture or vapors. A Brushless DC Motor should be installed in an environment free from vibration, shock, condensation, dust and electrical noise. Anaheim Automation carries a full line of IP65 Rated Sealed Brushless DC Motors for operation in harsh, humid environments.
NOTE: Any failure to observe the aforementioned safety and environmental precautions violates the manufacturing standards and intended use of the Brushless DC Motor, as well as it will void the warranty.
Troubleshooting a Brushless DC Motor
PLEASE NOTE: Anaheim Automation offers technical assistance free of charge to help the customer in product selection, installation, and servicing. However, while accurate guidance, technical data, and illustrations are intended to properly assist the customer regarding the Brushless DC Motor line and other products, such advice and documents are subject to change, and are solely supplementary. The customer is ultimately responsible for the appropriate selection and operation of their Brushless DC Motor system.
Problem: The Brushless DC Motor is running incorrectly, or stops running.
Solution: A Brushless DC Motor having difficulty operating could indicate that the Hall Sensors are bad. To check, use a resistor to pull up each Hall to 5 volts, and check each Hall with an oscilloscope while spinning the shaft. Monitor the point between the Hall and the resistor as pictured below in Figure 2.
Repeat this process for each individual Hall. When spinning the shaft manually, a low and high signal should appear on the scope. Keep in mind the importance of what value is used for the resistance; this depends on the amount of current the Hall sensors can withstand.
If this test demonstrates that the Hall Sensors are working correctly, the next step is to check the phases of the Brushless DC Motor. Hook up the Brushless DC Motor to a controller. With an oscilloscope, check each phase to see if a switching signal is present. If the phases do not pose a problem, this may indicate a bearing problem, or internal shorts. If these techniques do not seem to explain why the Brushless DC Motor is working improperly, the purchase of a new Brushless DC Motor should be considered.
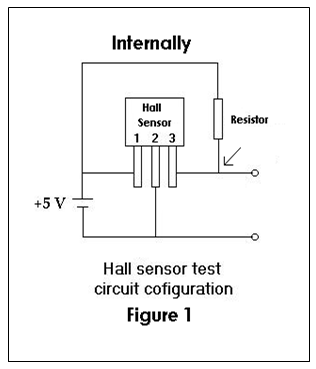
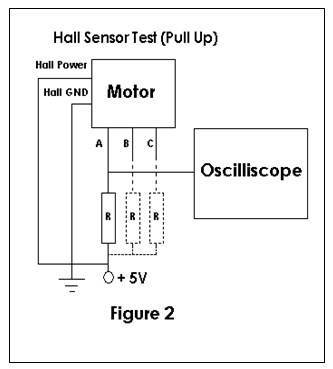
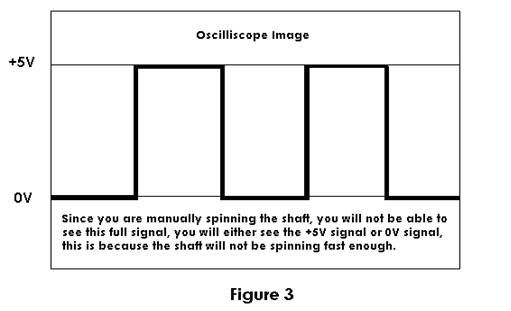

What is the Kt Constant in a Brushless DC Motor?
Winding Power = Kt*Kt/R
Kv = 1000 rpm / Vrms
Kt = oz-in / Amp
Kt = Kb * 1.35
Ke = Vrms / 1000 rpm
Kb = V / 1000 rpm
Back EMF = V/KRPM
History of a Brushless DC Motor
British scientist Michael Faraday first experimented with the idea of the electromagnetic induction motor in the early 1800's. By 1828 the DC Motor was introduced with three main components: the stator, rotor, and commutator. During that time, DC Motors did not contain permanent magnets. Instead, they operated similar to Brush DC Motors today, in that they had current flowing through the windings of the motor. In 1837 Americans Thomas and Emily Davenport transformed Faraday's DC Motor into one that could be used for commercial use. These DC Motors became popular in printing presses and powered machine tools. However, with the high cost of battery power, the demand was too small to keep them successful. In 1886, Frank Julian Sprague introduced the first practical DC Motor that was capable of constant speed under variable loads.
Over time, the elimination of the commutator and brushes made room for the introduction of electronic commutation. Although the Brushless DC Motor was quite expensive when first introduced, the advancements in design and materials drastically lowered costs and made the Brushless DC Motor a popular selection for many different applications.
Brushless Motor Quiz
1. What is the voltage constant?
2. What is the torque constant?
3. What is the stator?
4. What is the difference between Wye and Delta windings?
5. How do you find the voltage constant?
6. What happens when voltage is increased?
7. What happens when the voltage is decreased?
8. If you have two different input voltages and the same torque, what happens to the current and why?
9. How many phases are in a brushless motor?
10. What is the difference between a DC brushed motor and DC brushless motor?
Bonus Questions
11. How many pulses per revolution in a 4 pole and 8 pole motor for one hall sensor?
12. How do you change the direction of the motor by wire swapping?
Answers to Brushless Motor Quiz
1. What is the voltage constant?
RPM
Volts
2. What is the torque constant?
Torque
Current
3. What is the stator?
The stator contains coils of wire which will have voltage induced into them as the magnets pass over them.
4. What is the difference between Wye and Delta windings?
Wye windings give high torque at low rpm, and Delta windings give low torque at low rpm.
5. How do you find the voltage constant?
Take the No load speed and divide by the input voltage applied.
6. What happens when voltage is increased?
The speed of the motor increases as well.
7. What happens when the voltage is decreased?
The speed of the motor decreases also.
8. If you have two different input voltages and the same torque, what happens to the current and why?
The current will stay the same because of the Torque Constant. Torque is only relative to current, not voltage.
9. How many phases are in a brushless motor?
Three
10. What is the difference between a DC brushed motor and DC brushless motor?
A DC Brushed Motor needs only physical contact to pass current through its motor windings to allow commutations. A DC Brushless Motor needs a driver to commutate.
Bonus Questions
How many pulses per revolution in a 4 pole and 8 pole motor for one hall sensor?
4 Pole Motor has 2 pulses per revolution: 4/2 = 2 Pulses
8 Pole Motor has 4 pulses per revolution: 8/2 = 4 Pulses
12. How do you change the direction of the motor?
Switch around the Phases along with the Hall Sensors.
Brushless Motor FAQs
Q: Can different voltages be applied other than the specified voltage?
A: Yes, you can apply different voltages, although, you must keep in mind that there is a speed limit for the bearings. If you increase the voltage, the speed will increase. If you decrease the voltage then the speed will decrease. For example, if a Brushless DC Motor is rated to run at 3000 RPM no load with 36VDC, the motor will run 2000 RPM with 24VDC. The maximum speed, torque, and power are directly proportional to the voltage.
Q: How can I achieve a higher power output without purchasing a new motor?
A: This can be approached in two ways: increasing the voltage being applied or increasing the current being supplied to the motor. The equation:
Power = (Oz – in x ω) Power = Watts (W)
1351.2 ω = Speed (RPM)
Q: Do Hall Sensors need to be used to drive a Brushless DC Motor?
A: No, Hall sensors are only needed for feedback systems requiring a Hall Effect Sensor. A Brushless Motor may be sensorless where the back EMF is used to run the motor.
Q: What is Stall Torque?
A: Stall Torque is the amount of torque where the shaft ceases to move.
Q: What is Rated Torque?
A: Rated Torque is where the motor can operate continuously at a safe level.
Q: What is Peak Torque?
A: Peak Torque is where the motor can operate for a brief period of time, but will be damaged if run for longer periods.
Q: Can I run a Brushless DC Motor off of a battery?
A: Yes, along with a Brushless DC Controller.
Q: Can I run a Brushless DC Motor off of 110 VAC?
A: Yes, along with a Brushless DC Controller.
Q: Will a Brushless DC Motor slow down when the load is increased?
A: In closed-loop control, the Brushless DC Motor will not slow down, as long at the torque of the motor is strong enough. However, it will always slow down with open-loop control.
Q: Is it possible to burn up a Brushless DC Motor by giving it too much load?
A: Yes. It is protected if the controller has a current limit provision.
Q: What is the recommended cable distance between Anaheim Automation BLDC motors and drivers?
A: We recommend that the wiring between BLDC motors and controller not exceed 25 feet. Although it is not required, we suggest using Anaheim Automation shielded motor cable. This cable is ideally suited to handle all driver and motor combinations that we offer. We can also add connectors to the cables. Please contact an Applications Engineer for more details.
Q: Does Anaheim Automation sell encoders for BLDC motors?
A: Yes. We supply encoders for any size orders for customers that require a complete
motor/encoder assemble ready to mount. We can assemble the encoder to the motor for a nominal charge. Ask a Customer Service representative for more details.
Q: What is the life expectancy of Anaheim Automation BLDC Motors?
A: Anaheim Automation BLDC motors have a 20,000 hour life expectancy under normal operating conditions. Anaheim Automation's warranty is 12 months after the invoice date. See the "Environmental Conditions" sections of the BLDC motor guide for more details.
Q: Is there any damage caused by a BLDC motor that is disassembled?
A: Yes, and it will void your warranty! If you have a motor failure, or are concerned about the performance, contact Anaheim Automation. Please note that the warranty period is 12 months from the date of invoice.
Q: My motor stalls at high speed when the temperature exceeds 65 degrees C. Why?
A: Try to keep the BLDC motor below 60 degrees C or move up one stack length in your motor.
Q: Are BLDC motors with keyway, shaft-flat, cables and encoder-ready features considered "special"?
A: Yes, they are considered a "special", non-stock item and may require a NRE or SET-UP charge. There is an additional cost for some changes as well. Sometimes the NRE and SET-UP charges are waived if the volume of the order is great enough.
Q: Can I get a BLDC motor and Speed Controller assembled together?
A: Yes. In NEMA sizes 17 and 23, we offer an Integrated BLDC Motor with Controller product. Check our BLYMD, BLWR23MD, BLWR23MDA, BLWS23MD and BLWSMDA series for more details.
Q: Can I add an encoder to BLDC motors?
A: Optical encoders can also be added to a Brushless DC Motor, allowing both direction and speed to be determined. More precise applications may use Optical Encoders with a third index signal, to determine pulse per revolution.
Q: Is any maintenance required for a BLDC motor?
A: Due to the lack of brushes or a commutator, there is nothing to replace within a BLDC Motor, making it extremely low maintenance. The only requirement is that the motor be used in accordance with its published specifications, and in a clean environment to ensure it does not overheat or result in system failure.
Q: Are there any environmental considerations I should be aware of to operate a BLDC motor and controller?
A: Precaution must be taken by the user with respect to the environment of the BLDC motor during operation, repair, and service. The environment in which a BLDC Motor is used must be conducive to good general practices of electrical equipment. Do not run a BLDC motor near flammable gases, dust, oil, vapor or moisture. The BLDC motor must be protected by a cover if operated outdoors, ensuring the motor receives adequate air flow and cooling. Any presence of moisture may result in system failure and/or electric shock. Therefore adequate care should be taken to avoid any interaction between the motor and any kind of moisture or vapors. A BLDC motor should be installed in an environment free from vibration, shock, condensation, dust and electrical noise. Anaheim Automation carries a full line of IP65 Rated BLDC motors for operation in harsh, humid environments.
Brushless Motor Glossary
Armature – One of the components of a Brushless DC Motor, the armature is part of the permanent magnet or electromagnet, or the moving iron part of a solenoid or relay. The other component is the field winding or field magnet. The role of the "field" component is simply to create a magnetic field (magnetic flux) for the armature to interact with, so this component can comprise either permanent magnets, or electromagnets formed by a conducting coil.
Accessory Shaft - The rear side shaft of the motor, sometimes referred to as a "double-ended" motor.
Back EMF (Back ElectroMotive Force) - The voltage, or electromotive force, that pushes against the current which induces it. Back EMF is one of two ways of locating the position of the rotor in speed control. The type of controller that utilizes this method is known as sensorless control.
Brushless DC Motor – An electronic synchronous motor, powered by a DC current, and operated by means of electronic commutation.
Commutator - A rotary electrical switch that periodically reverses the current direction between the rotor and the external circuit.
Controller (Sometimes referred to as a Driver or Electronic Speed Controller) - An electrical circuit or other electronic component used to control another circuit. A Brushless DC Motor Controller acts to control the direction and speed of the motor, or perhaps act as a brake. The Brushless DC Motor Controller is crucial to the operation of a Brushless DC Motor.
Delta Configuration (or Pi) - The Delta Configuation gives low torque at low RPM. The resistance between any two points is a series-parallel combination of all three resistors. Therefore, the effective resistance of the circuit will be less than the values of the individual resistors involved. This can be very useful in situations where it is desirable to use larger resistance values than the circuit would normally require.
Electric Motor - An electric motor is a type of engine which uses electrical energy to produce mechanical energy.
EMF (ElectroMotive Force) - EMF is the external work expended per unit of charge to produce an electric potential difference across two open-circuited terminals.
Hall Effect Sensors - A Hall Effect Sensor is a transducer that varies its output voltage in response to changes in magnetic field. Hall sensors are used for proximity switching, positioning, speed detection, and current sensing applications.
Inrunner - An Inrunner Motor is a type of Brushless Motor where their rotational core is contained within the motor's can, typically used in RC automotives and aircrafts.
Outrunner - This type of Brushless Motor spins its outer shell around its windings, typically used in RC automotives and aircrafts.
Rotor - The rotating part of the Brushless DC Motor, operating with a stationary element called the stator. The rotor positioning is important regarding speed control of the Brushless DC Motor.
Stator - The stator contains the coils of wire which have voltage induced in them as the magnets pass over them. The stator is the stationary part of the Brushless DC Motor.
Wye (Y or Star) Configuration - The Wye Configuration provides high torque at low RPM, but not as high top RPM. The resistance between any two of the three external connections will be the series combination of two of the three resistors.