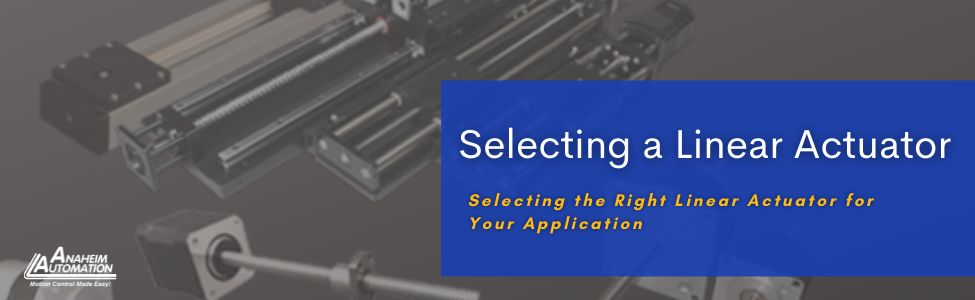
Selecting a Linear Actuator
Selecting the Right Linear Actuator for Your Application
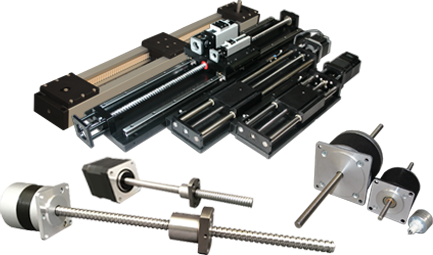
Linear Actuators Basics
Linear actuators are used in a variety of applications across numerous industries, including medical equipment, agriculture machinery, high-voltage switch gears, train and bus doors, and factory processes and assembly machinery. Typical use cases include medical beds, patient lifters, wheelchairs, adjustable tables and workstations, and diagnostics, to name a few.
Each linear actuator application has unique requirements. Manufacturers throughout the world offer innumerable models of linear actuators in a wide variety of stroke sizes, speeds, voltage and types. With the availability of so many manufacturers, models and options, selecting the right linear actuator for your application can be a daunting task.
When a system is tailored for an application, the specific requirements will influence both the design and the manufacturing processes. Regardless of end use, an actuation system is designed by first identifying basic needs, then evaluating certain key parameters that ultimately affect the overall system operation.
Electromechanical linear actuators are designed to provide precision, efficiency, accuracy, and repeatability in effecting and controlling linear movement. These devices serve as practical, efficient, and relatively maintenance-free alternatives to their hydraulic or pneumatic actuator counterparts. Depending on type and manufacturer, today's electromechanical linear actuators can handle loads up to 3,000 pounds (13 kilonewtons) and deliver speeds up to 100 inches/second (2540 millimeters/second), with strokes ranging from 2 inches (50 millimeters) to 60 inches (1,500 millimeters).
Actuators can be self-contained in aluminum, zinc, or polymer housings and ready to mount for easy plug-in operation (using either AC or DC power supplies). What's more, actuators featuring both modular design and open architecture enable interchangeable internal and external components, according to specifications. Please note that standard components – including the types of drive screws, motors, front and rear attachments, controls, and limit switches used – will allow for desired customization without the costs typically associated with special modifications.
Having of a basic understanding of the typical use-cases for the various types of electromechanical linear actuators may be a good starting point.
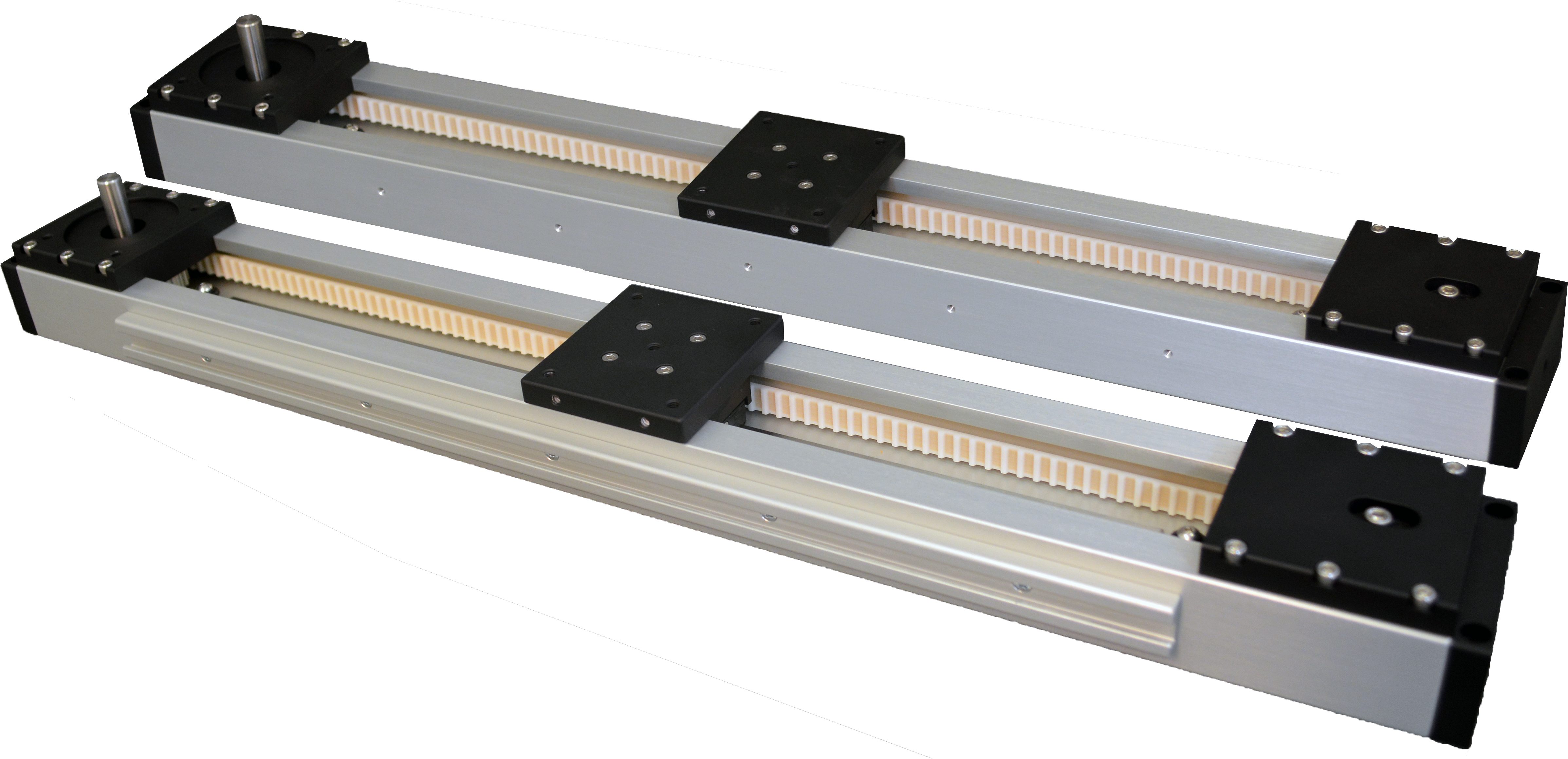
Belt-driven linear actuators are designed for high speeds and light loads, and are suitable only for low-inertial loads. Common applications for belt actuators include automated windows and doors, high-speed data acquisition, and scanning devices.
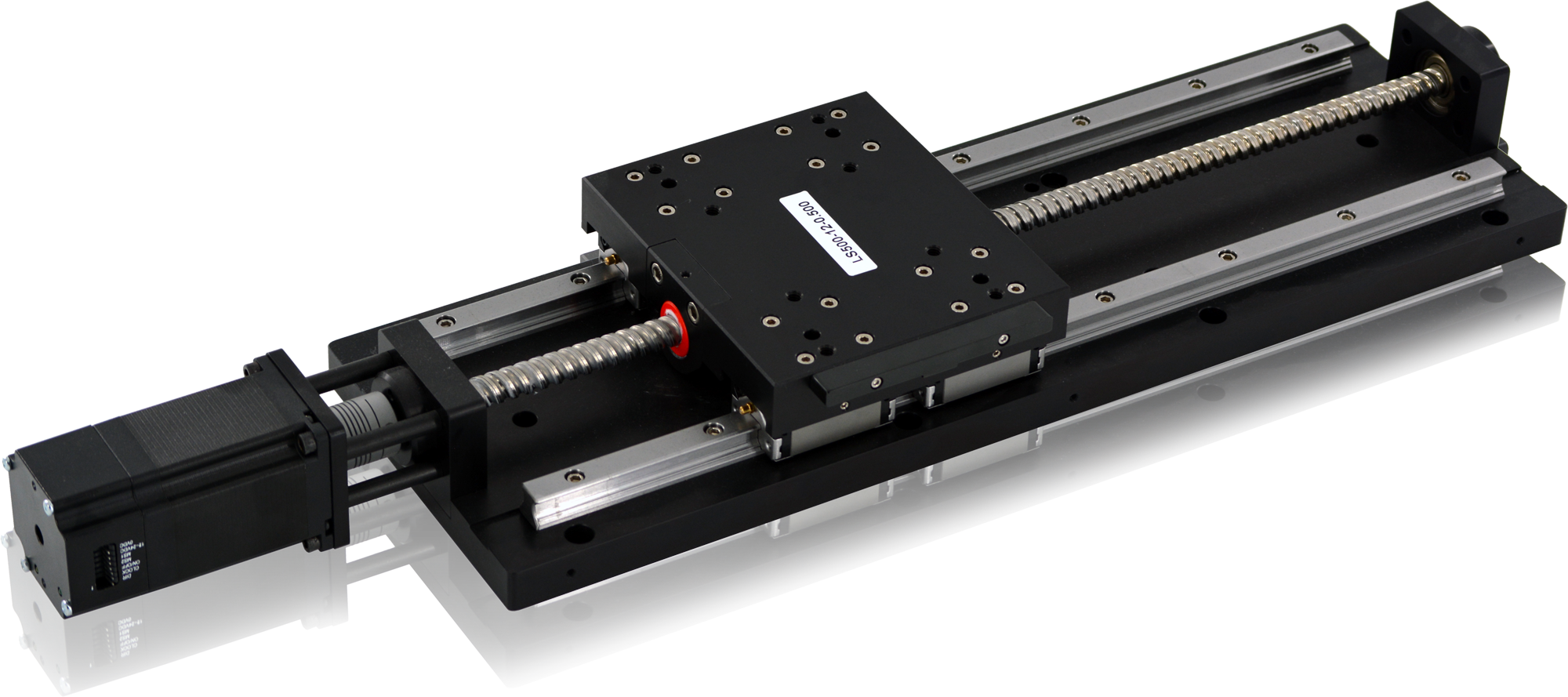
Screw-driven linear actuators are suitable for low speeds, heavy loads, and high-inertial loads. These devices are typically used in positioning equipment, CNC machines, and anywhere else slow point-to-point movement is required.
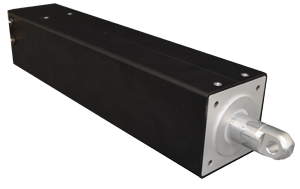
Rod-style linear actuators excel at lifting and thrusting applications, with thrust-bearings built into the actuators themselves. They are similar to screw-driven tables in terms of speed, load, positioning, and accuracy capabilities. Rod actuators offer a compact, collapsible design great for projects where space constraints are a concern.
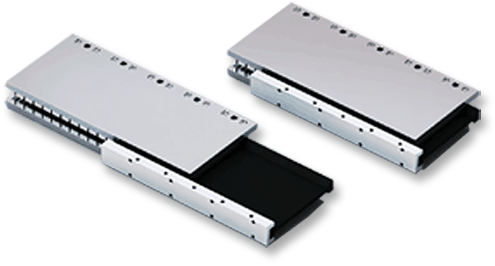
Linear servos are capable of bearing heavy loads at a wide range of speeds (1 to 3,000 mm/sec) and are able to handle high-inertial loads while delivering accurate force. Linear servos are typically used in high-precision, heavy-load and high-inertial load applications, as well as in precision-torque and positioning applications.
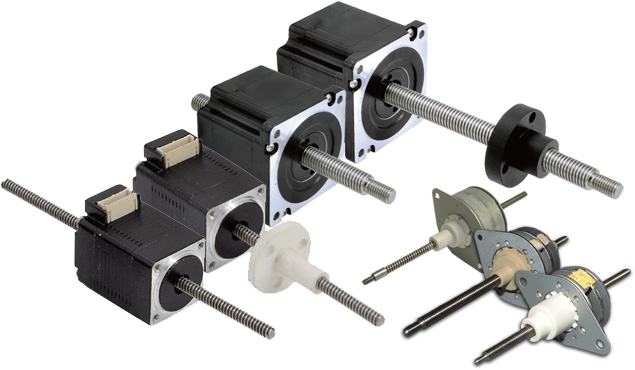
Stepper Linear Actuators are intended for point-to-point positioning applications. This type of actuator is best suited for applications with light loads and slow speeds. Steppers are open loop accurate, so they do not require an encoder for accurate positioning.
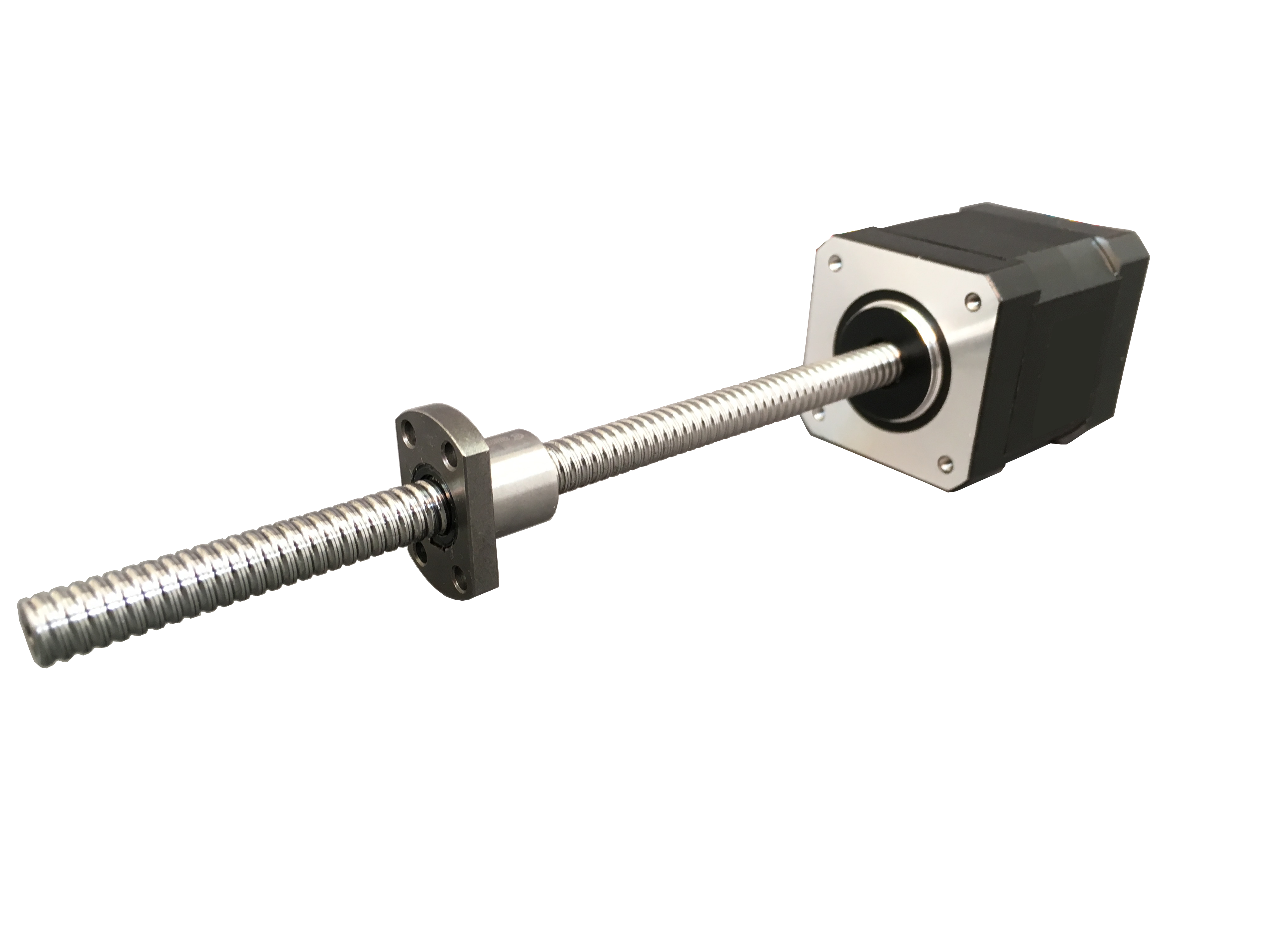
Brushless DC Linear Actuators are great for high-speed motion. Their specialty is delivering power at high speeds, rather than the high accuracy of a stepper. Brushless linear actuators may require an encoder to obtain accurate positioning data.
Starting the Process
Step One: The Basics
Discuss your application in as much detail as possible with a knowledgeable and experienced supplier. At this stage, focus on basic specifications for load, actuator type, power, and control type in the selection process:
Force and Direction
How much force (in newtons or pounds-force) and in which directions (push, pull, vertical, and/or horizontal) will the actuator need to move? Note: Force is a function of maximum and average dynamic loads.
Distance or Travel
How far will the actuator need to move? This will factor in both the stroke and retracted lengths, and is usually expressed in millimeters.
Speed
How fast (millimeters/second or inches/second) will the actuator need to move?
Duty Cycle
How often will the actuator operate, and how much time will elapse between operations? This refers to the "duty cycle," which will be based on the number of expected repetitions per unit of time in hours/day, minutes/hour, and/or strokes/minute.
Lifetime
What is the desired lifetime for the end product? This will impact virtually every component within a linear actuator system.
Installation
How will the actuator be mounted? Will front and/or back mounts require special configurations?
Safety Features
Does the application suggest particular safety mechanisms (e.g., "manual operators" for use in case of emergency)?
Environment
Will environmental factors (temperature variations, moisture, vibration, or end-product shock) pose a challenge to operation?
Footprint
Is space limited? If so, the actuator will have to be designed to fit in a specific footprint.
Power Supply
What are the power supply options needed – AC, DC, voltage, wattage? Can you use a battery, or does the power supply or control need to be plugged into a utility source? Depending on the motor control or motor type, different voltages and types are needed.
Feedback
Is feedback required for speed and/or position? This will indicate a need for add-on components, such as encoders.
The specific parameters that play a crucial role in every electromechanical actuator application are: electrical power in, duty cycle, and actuator efficiency.
Step Two: The Power Factor
A linear actuator is a device that produces linear motion by utilizing some external energy source. The source of energy can be piezoelectric, pneumatic, hydraulic, mechanical, electro-mechanical, etc. A linear actuator system draws principles from both electrical and mechanical engineering disciplines.
Power (defined in watts) is usually the first requirement to be calculated. In order to get mechanical power out of an electric linear actuator, it's necessary to put electrical power into the system. Mechanical power out is usually the easier of the two to define because all that's needed for its calculation is the force, or the load that will be moved, and the speed required.
If the parameters are in metric (SI) units, multiply the force (in newtons) by the speed (in millimeters/second) to obtain watts. (To convert pounds to newtons, multiply by 4.448; to convert inches to millimeters, multiply by 25.4.)
Mechanical power out (Po):
Po = F x v
F = Force (N)
v = Velocity (meters/sec)
Information regarding electrical power can be ascertained through performance graphs and charts from suppliers' specification sheets. Suppliers chart this information differently from one another, but more often than not, there are graphs for force vs. speed and force vs. current draw at a specified voltage. This data is often presented in two graphs, or combined in one. The current draw may also be presented in a table. In addition, factors will be given based on a duty-cycle curve. The relevant formula is as follows:
Electrical power in (Pi):
Pi = E x I
E = Voltage (V)
I = Current (A)
Step Three: Calculating Duty Cycle
Users will need to establish the duty cycle factor (sometimes called the "derating factor") for the linear actuator application. Duty cycle is important. Sometimes the preliminary actuator selection may not meet all of an application's operating requirements. The duty cycle indicates both how often an actuator will operate, and how much time there is between operations.
Because the power lost to inefficiency dissipates as heat, the actuator component with the lowest allowable temperature (usually the motor) establishes the duty-cycle limit for the complete linear actuator system. Please note – there are some heat losses from friction in a gearbox, and via ball-screw and acme-screw drive systems.
To demonstrate how the duty cycle is calculated, assume an actuator runs for 10 seconds cumulative, up and down, and then doesn't run for another 40 seconds. The duty cycle is 10/(40+10), or 20%. If duty cycle is increased, either load or speed must be reduced. Conversely, if either load or speed decreases, duty cycle can increase.
The duty cycle is relatively easy to determine if a linear actuator is used on a machine or production device. In less predictable applications, or those where the linear actuator will be used infrequently, it's advisable to estimate the worst-case scenario in order to assign a meaningful duty-cycle calculation. It is not advisable to operate on the edge of the manufacturer's power curves, because this might cause the linear actuator and other components to run too hot. However, in some applications where the duty cycle is 10% or less, the actuator can run to the limit of its power curves.
Step Four: Ascertaining 'Efficiency' and Expected Life
A system's "efficiency" is usually missing from most manufacturers' literature, but it can tell the user how hot the actuator may get during operation, whether holding brakes should be specified in the system if the actuator uses a ball screw, and how long batteries may last in battery-powered systems, among other pertinent data. Calculating efficiency from performance curves is simple: Divide mechanical power out by electrical power in. This yields the efficiency percentage.
While these factors are being calculated, and decision-making is moving toward final selection, one additional parameter should be addressed: the application's expected lifetime. Although linear actuator components (e.g., the motor or screw) can be replaced, most actuators can't be easily repaired. In addition, it's important to cover application life expectancy because suppliers will sometimes indicate acme or ball screw life at a certain load, or include mathematical formulae to calculate life based on application parameters. A good design practice is to strive to have the screw and motor life expectancies match as closely as possible.
In those cases where an existing linear actuator must be replaced, ensure that the application engineer has all the necessary information to ensure a good fit. Whenever a linear actuator is subject to replacement, it is recommended to review the application as if it were new.
Other Selection Considerations: Budget and Experience
Having a clear picture of a linear actuator system budget in your mind will help in selecting the best product at an affordable price. Budget planning in advance can save considerable time in the selection process by eliminating some types that are too expensive for the application.
While there are many companies providing linear actuators in the market today, it is critical to choose a reliable supplier for the best results. Working with a knowledgeable and dependable supplier ensures expectations are met and headaches avoided. An experienced supplier can be trusted to deliver the features and performance you need for your system, at the right price for your budget.
Since 1966, Anaheim Automation has helped customers across a wide spectrum of industries – with diverse application needs – source the right solutions for their designs. With over 55 years of expertise in the motion control industry, Anaheim Automation is a partner you can trust for your linear actuator needs.
Need Application Assistance?
For help selecting the ideal linear actuator for your requirements, with all the right options, contact an Anaheim Automation applications engineer.