- Precise Control
With Network Synchronization using distributed clocks, the EtherCAT Network
can be used as a reference clock for the whole network. Kinco Servo Drives
support 5 control modes: Homing Mode, Profile Position Mode, Profile Velocity
Mode, Digital Interpolation, and Synchronized Position Mode. - Versatility and Functionality
EtherCAT, an open network based on Ethernet, achieves real-time,
high-speed, synchronized control through efficient network topology,
avoiding overly complicated network structuring. - Ease of Use
Free, Easy-to-Use Software shortens prototyping time.
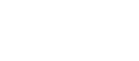
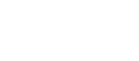
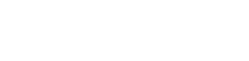
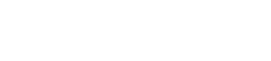
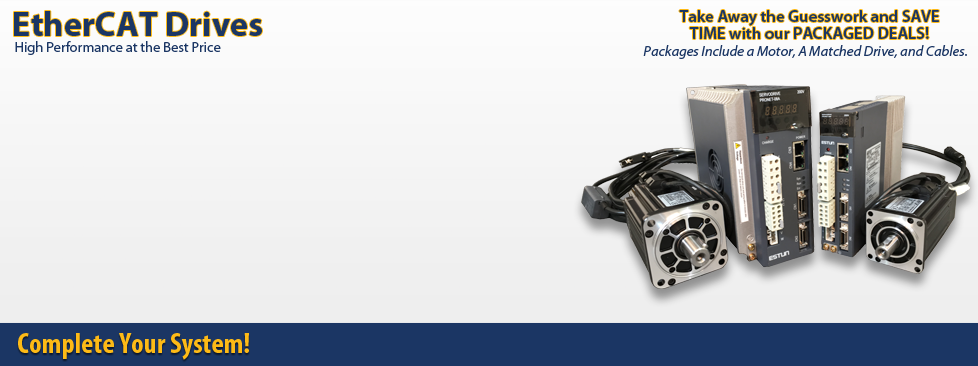

Item ↑ ↓ |
Rated Power (Watts) ↑ ↓ |
Rated Voltage ↑ ↓ |
Drive Control Capabilities ↑ ↓ |
COMM ↑ ↓ |
I/O Signals ↑ ↓ |
Downloads | Price (USD) ↑ ↓ |
Quantity Discounts |
Stock Status ↑ ↓ |
Add To Cart |
---|---|---|---|---|---|---|---|---|---|---|