Anaheim Automation offers a wide variety of high-performance AC servo motors and drives. They are perfect for both low and high volume requirements, at competitive prices that make servos surprisingly affordable! Motors and drives can be purchased separately, or, select a system which offers a matched motor, drive, and cables in one discounted package - reducing errors, wiring time, and cost! With friendly customer service and professional applicationassistance, Anaheim Automation often surpasses the customer's expectations for fulfilling specific motion control requirements.
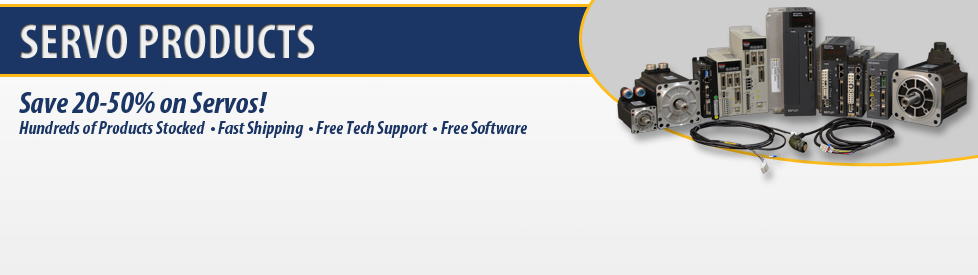
- Maximum Speeds from 1,500 to 6,000 RPM
- Power from 50 to 5,000 Watts
- Frame Sizes from 40 to 180mm
- Rated Torque from 22 to 5,438 oz-in
- Rated Current from 0.7 to 28 Arms
- Power from 50 to 5,000 Watts
- Position, Speed, and Torque Control
- MODBUS, EtherCAT, and CANopen Communication Protocols
- Rated Voltage from 24 to 70 VDC or from 88 to 253VAC Input
- Power from 50 to 5,000 Watts
- Motor Frame Sizes 40mm to 180mm
- 24-70VDC, Single-Phase 120/240VAC, or Three-Phase 240VAC Input
- Free, Easy-to-Use Software
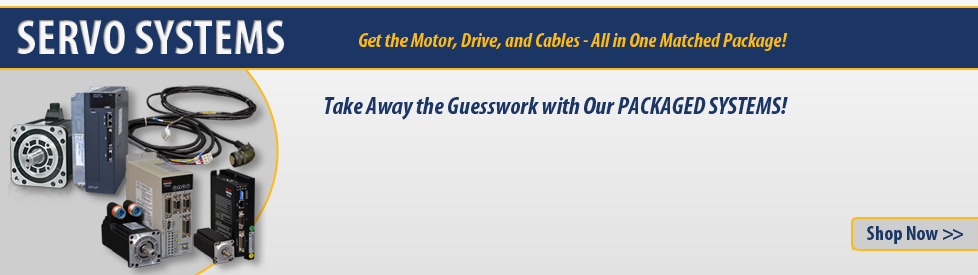
- Power Rating from 50W to 2kW
- High Communication Speed
- Precise Multiple Axis Synchronous Control
- Supports 32- Segment Position Table Feature
- 24-70VDC or 220VAC Single Phase Input
- Ideal for Robotics, Machine Tools, Logistics, and Packaging Industries
- Drive Profile: Homing Mode, Profile Position Mode, Profile Velocity Mode, Digital Interpolation and Synchronized Position Mode
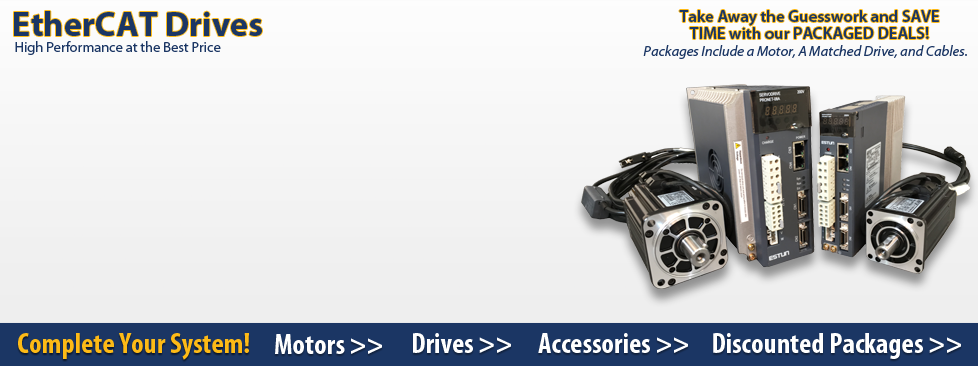
- Up to 961N Peak Force
- Fit Any Length Requirement
- Continuous Power from 26 to 629 Watts
- Designed to Eliminate Backlash, Wear,
and Maintenance
- Handheld Controller for Use with the EDC
Servo Drives - Power, Feedback, and Communication Cables
- I/O Control Cables are Available in Addition to a 50-pin Break Out Board